探秘保時捷萊比錫工廠:德國零影響工廠長什麼樣?
郝倩/發自德國萊比錫
前兩日去了德國萊比錫,在這個德國東部的保時捷工業基地進行了連續兩日的持續走訪。德國東部不算德國最富裕的地方和傳統工業基地,卻是因為斯圖加特,慕尼黑這些富庶之地的德國大企業的擴張而受益頗深。
作為一家從2000年奠基,2002年開始投產的“新工廠”來說,這20年保時捷萊比錫工廠一直在投資,擴產和完善的過程中。與斯圖加特老根據地70多年曆史的祖芬豪森的工廠相比,新生產基地擁有更大的想像空間,也更容易打造一個用以完善“生態鏈”的體驗中心。這裏還是一個“零影響工廠”,算是德國人理想中的工廠樣本。
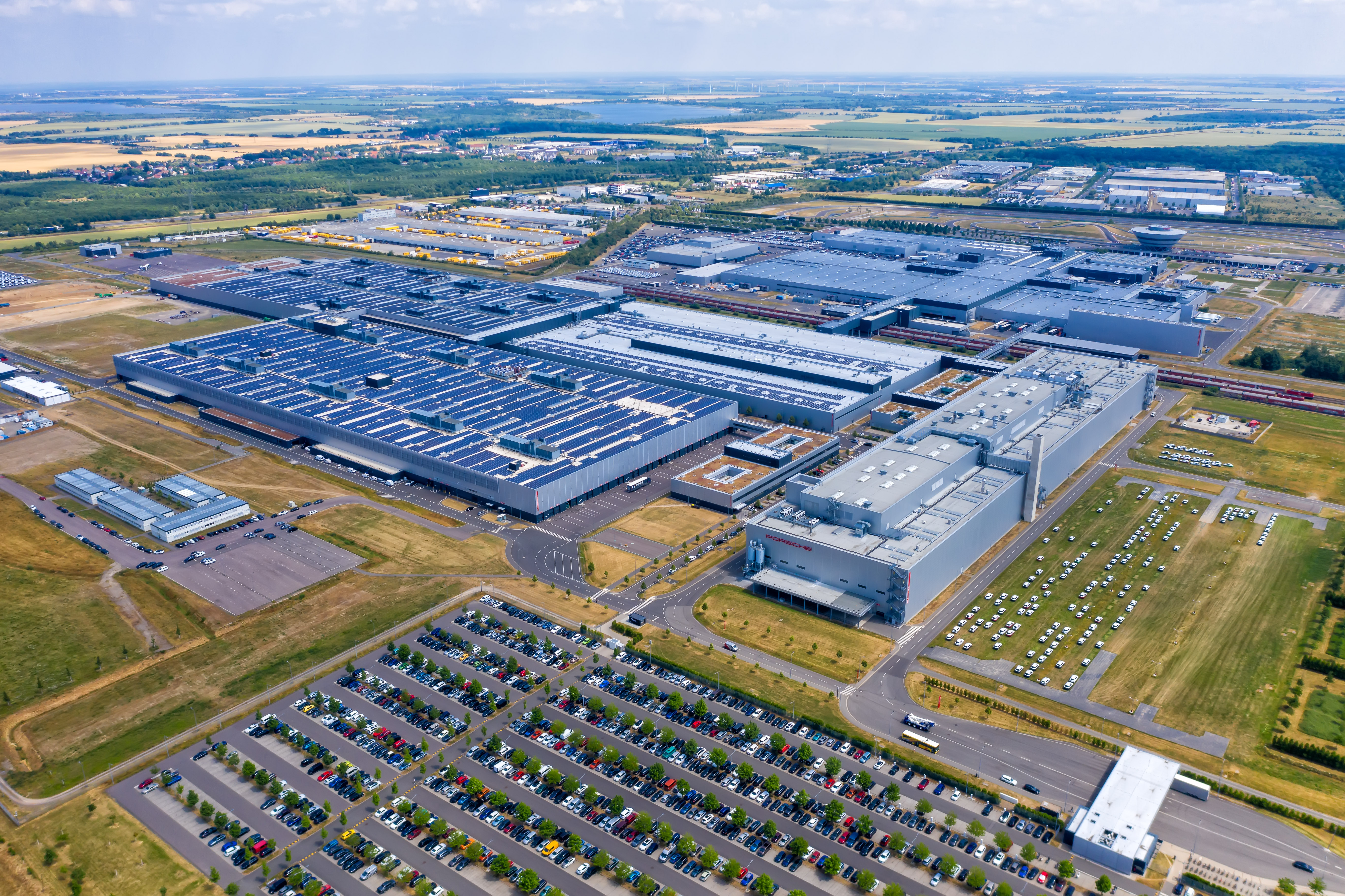
在我看來,萊比錫的保時捷工廠都不應該被稱之為“工廠”或者“生產基地”,而更像一個保時捷打造的完整生態系統。這裏有保時捷最現代化的工廠,純電,混電和傳統內燃機車型的全面共線生產。他們還有測試賽道,越野賽道,甚至還有一個幾乎不受打擾的,和很多野生動物共同生活的“自然保護區”……更誇張的是,工廠本身也可以對公眾開放,預約參觀,中心位置的體驗中心可以試車,可以預約午餐晚餐,還可以定製賽車體驗課程,一家人的叢林探險。
此時你才能體會到,原來一個品牌的意義,不僅在於產品的品質本身,還有圍繞產品的客戶和潛在客戶,以及“發燒友們”。在保時捷的故事中,這種吸引力圍繞著汽車動力,賽道體驗以及探討動力的極限在哪裡,是某種夢想的體現。這才能完整構成一個品牌的“生態系統”。
——如何讓機器和人工完美融合
我此次完整參觀了保時捷萊比錫工廠的重要車間,從車身組裝開始。一個車身大約重達400公斤,車身的每一個部件有不同的材質構成。舉例來說,Panamera車身重420公斤,車身部件的生產基地就在萊比錫附近,電池包由附近的德國公司DRAXLMAIER提供。電動發動機和傳統內燃機則是由保時捷在斯圖加特的工廠生產。這都是保證供應鏈足夠緊湊。
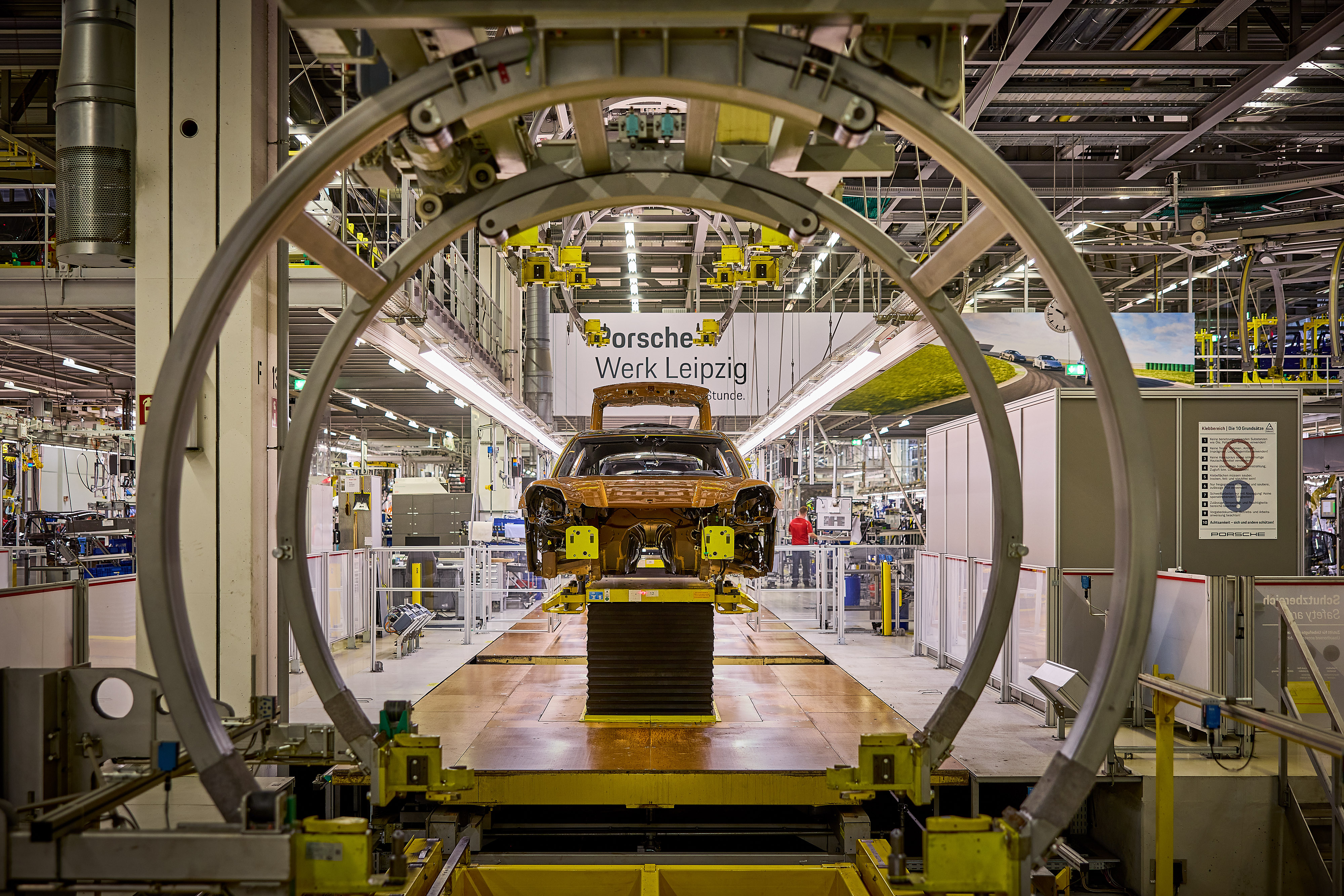
車身車間廠房面積從3.5萬平方米,需要超過380個高精度工業機器人。之後擴建的Panamera車身車間9.1萬平方米,擁有70個的無人運輸車,無需地面標籤,可以獨立行駛。這些無人運輸車之間還可以相互溝通。
車身車間的下一站是6萬平方米的噴漆車間,以及5.4萬平方的組裝車間。車身組裝和噴漆車間自動化程度可以高達95%左右。
完成4層噴漆之後,最終噴漆的厚度共0.13mm,小於一根頭髮絲的厚度。噴漆車間高度自動化,就連之前要靠人工拍照進行質量檢測環節都已經通過機器拍照代替。每天機器拍照5500萬張,既可以快速檢測出車身噴漆的瑕疵,又可以在進行圖片重疊之後,找到噴漆環節中的不足,用以改善生產流程。
之後是組裝車間。一輛車要在組裝車間完成組裝,需要走過3.6公里的生產線。為了讓每一步都能夠及時完成,每一個工作太多需要的零部件都要按時按序由“機器人”提前運送到位。比如,每天需要安裝的輪胎會在安裝前4個小時從供應商下單。
在組裝車間,通常一個工作團隊12個人,分管5個工位。他們可以輪流替換,保證每個人都可以獲得一定的休息時間。這其中的邏輯就是“員工身體健康,才能保證生產質量”。
同時,和大多數德國現代化工廠一樣,需要人力的每一個生產環節都要考慮到人體力學。為了方便工人組裝,車身會在機器的控製下翻轉旋轉90度。為了讓安裝工作更加對人體友好,有的工作台還採用木質地板,踩著工作舒適度增加。
比如,讓我印象深刻的其中一個環節,就是如何是給車裝擋風玻璃。這個環節是完全由機器手臂完成。貼玻璃大概需要2分鍾,5分鍾後粘合劑固化,20分鍾後完全固化……每一步都是精確控製的。
——電氣化背景下的共線生產
保時捷工廠設計的精妙之處,就在於“按需生產”,以及“靈活共線生產”。這種所有車型和一個車型不同動力車型,以及各種定製化要求都要在一條生產線完成。“共線生產”最大的問題,就是會大大提升生產系統的複雜度,但只要可以實現,就可以保證生產率,也是效率最高的生產模式。因為工廠不會因為某種動力車型的訂單減少就要減產或者停產,保證工廠可以一直高效運營。
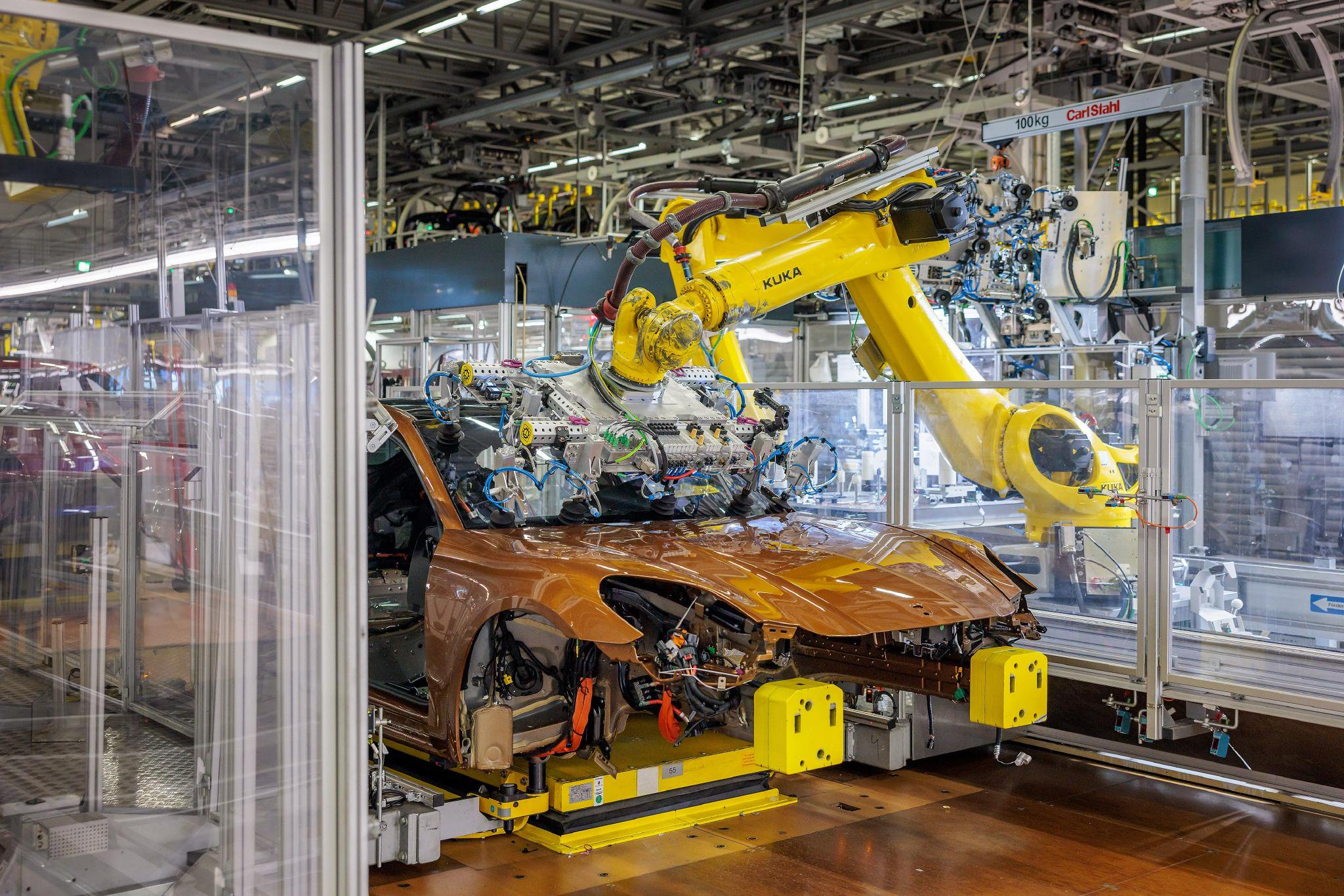
並線生產後,一台車從車身到下線平均需要2天時間。比如,Macan車型就正好需要兩天,Panamera需要1.5天。
電車和傳統內燃機在裝配過程中的區別,主要在於電車的驅動系統更為複雜,需要更多傳感器。傳統內燃機車裝配則需要更多原件,也需要多些工位。所以每條線都有智能生命週期系統,根據銷售情況進行產量規劃。這種規劃需要細緻到每一個工位需要多少時長,配備幾名員工。
保時捷去年賣了4萬多輛純電跑車Taycan,2030年力爭達成 80% 以上銷售新車為純電車型的目標。這個目標沒改變,但目前的形勢確實有些微妙。
就像很多德國車企眼下的顧慮:電氣化戰略不能變,可誰也不確定電氣化轉型這個“過渡期”最終需要多久。在這個“不確定會多長”的過渡期里,工廠生產燃油車和電動化車型的數量,需要根據市場的情況進行即時的調整。只有這樣才能避免因為供需比例不匹配讓某些產品線停工。
所以最優的解決方案,就是所有車型,以及所有車型中的內燃機車型、插電式混合動力車型以及純電動車型,統統並線生產。這也是為了在生產端,提供對於市場需求反應的高度靈活性。這種生產操作模式需要更為精密複雜的生產管理流程,但總體來看確實可以最大程度提升生產效率。
保時捷全球首席財務官麥思格表示(Lutz Meschke)說:“我們沒有辦法預測未來,但需要密切關注每一個市場的需求和發掘潛力。現在在中國,電動車發展很快。但是在歐洲和美國,電動車發展速度可能有所放緩。我們認為中國市場未來增長潛力巨大。”
——“零影響”工廠有哪些要素
萊比錫工廠有很多新鮮的概念,比如他們可以做到在整個產業鏈實現“零影響”(zero-impact)。除了零排目標,還有綠色電力,循環經濟。從2017年開始,萊比錫工廠100%採用綠色電力,2021年實現生產淨碳中和。
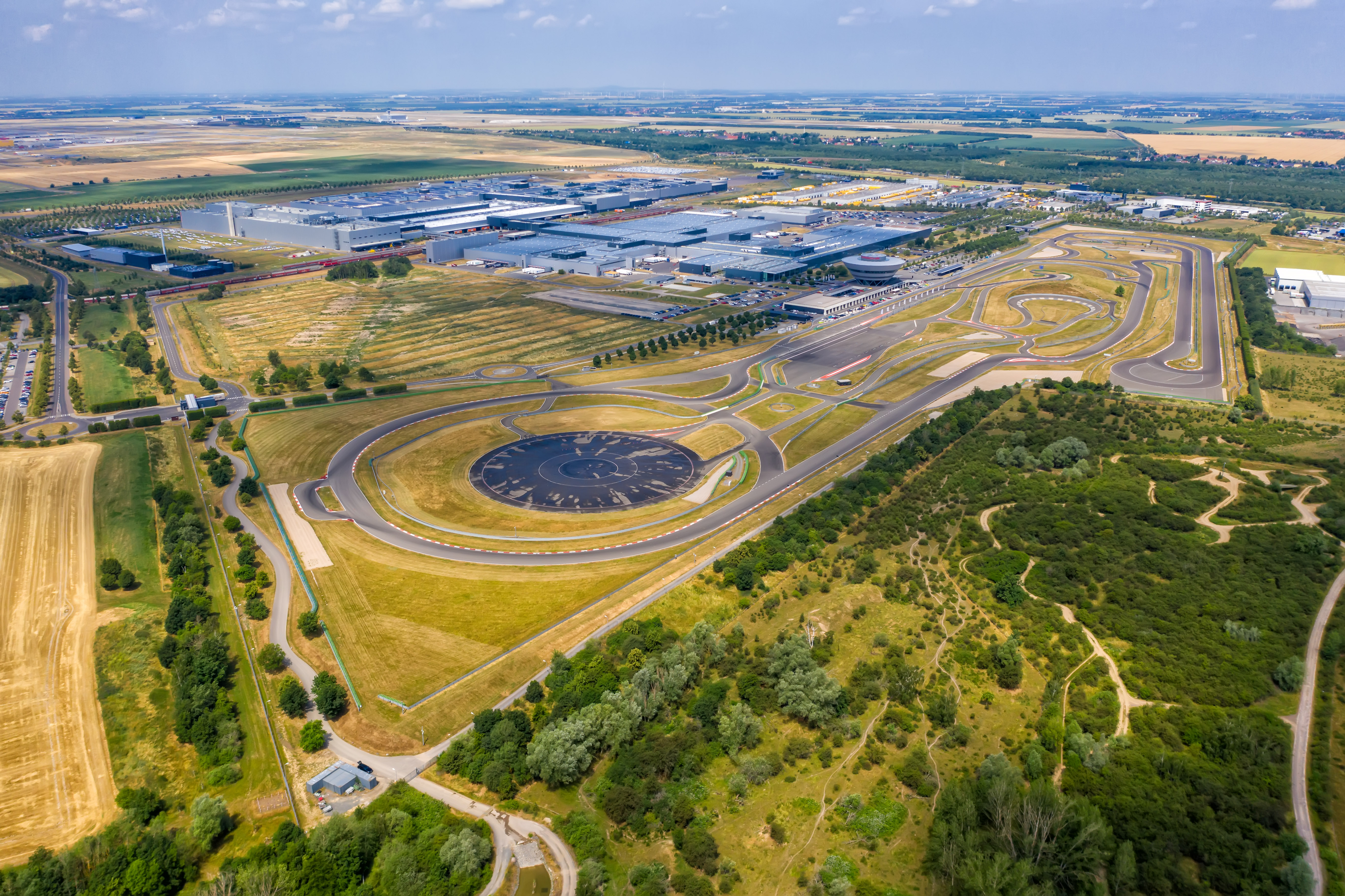
綠色精益生產有幾個具體的例子:第一,廠房屋頂使用太陽能發電板,每年光伏系統發電量89萬千瓦時。其次,50%的供熱能量來自生物質,也是一種可再生能源。而噴漆車間的餘熱,也會在之後收集進行再利用。這種“熱能再利用”在歐洲很多先進工廠都有,是一個重要的考量因素。
第三是對生物多樣性的推動。保時捷越野賽道占地132公頃,與多種植物和野生動物和諧共生。所以當保時捷發燒友來到越野賽道體驗各式不同路況時,遠遠看著他們的觀眾,可能就是一些野生動物。但賽道的設計也會保證不要打攪到野生動物的棲息地。
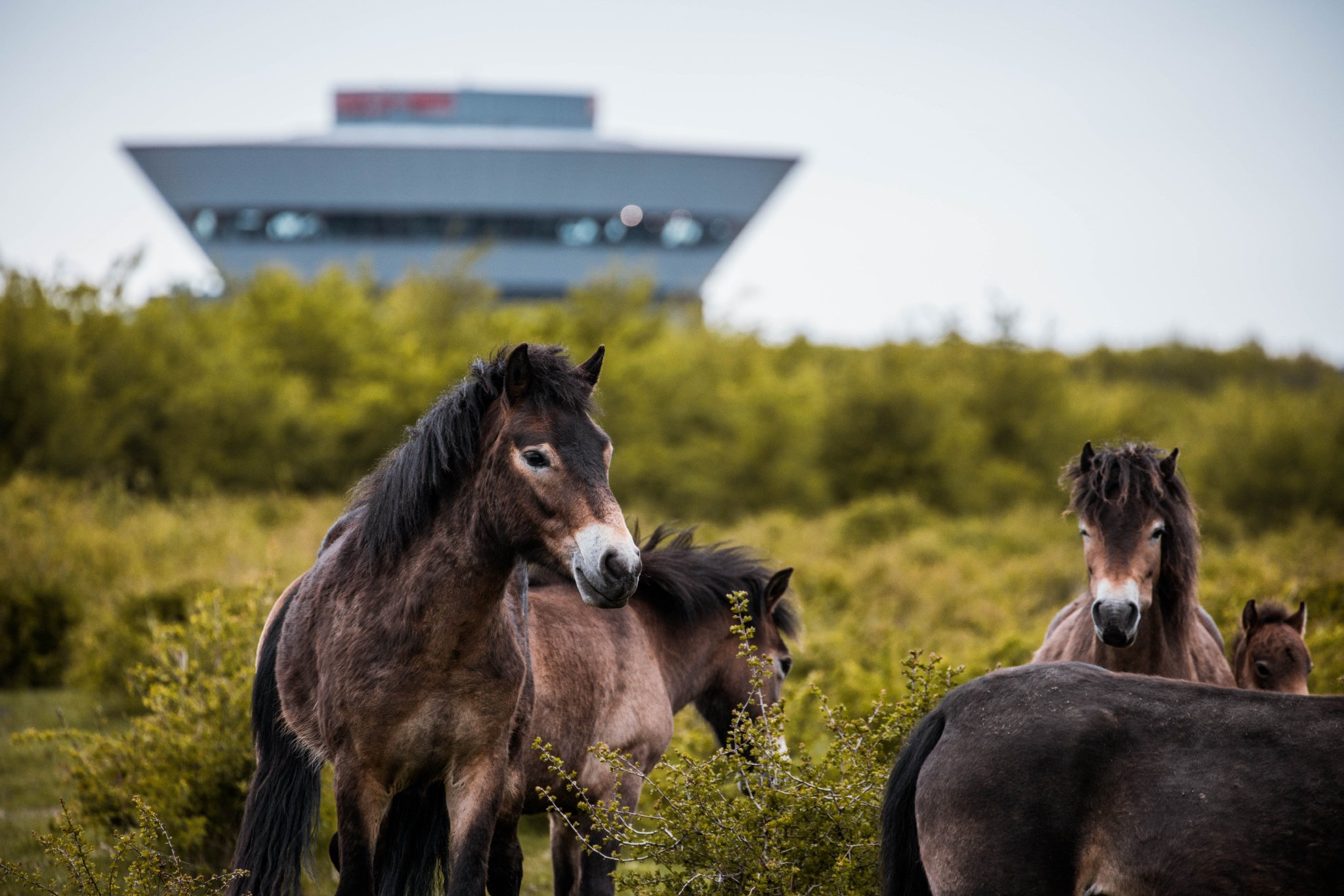
還有一個有趣的故事。2017年開始,萊比錫工廠引入300萬隻蜜蜂,生產自己的蜂蜜,年產量500-800噸。這些對於生態的保護又讓保時捷工廠可以做很多有趣的賽道駕駛,家庭森林探險發現的項目,形成了很獨特的“生態系統”。
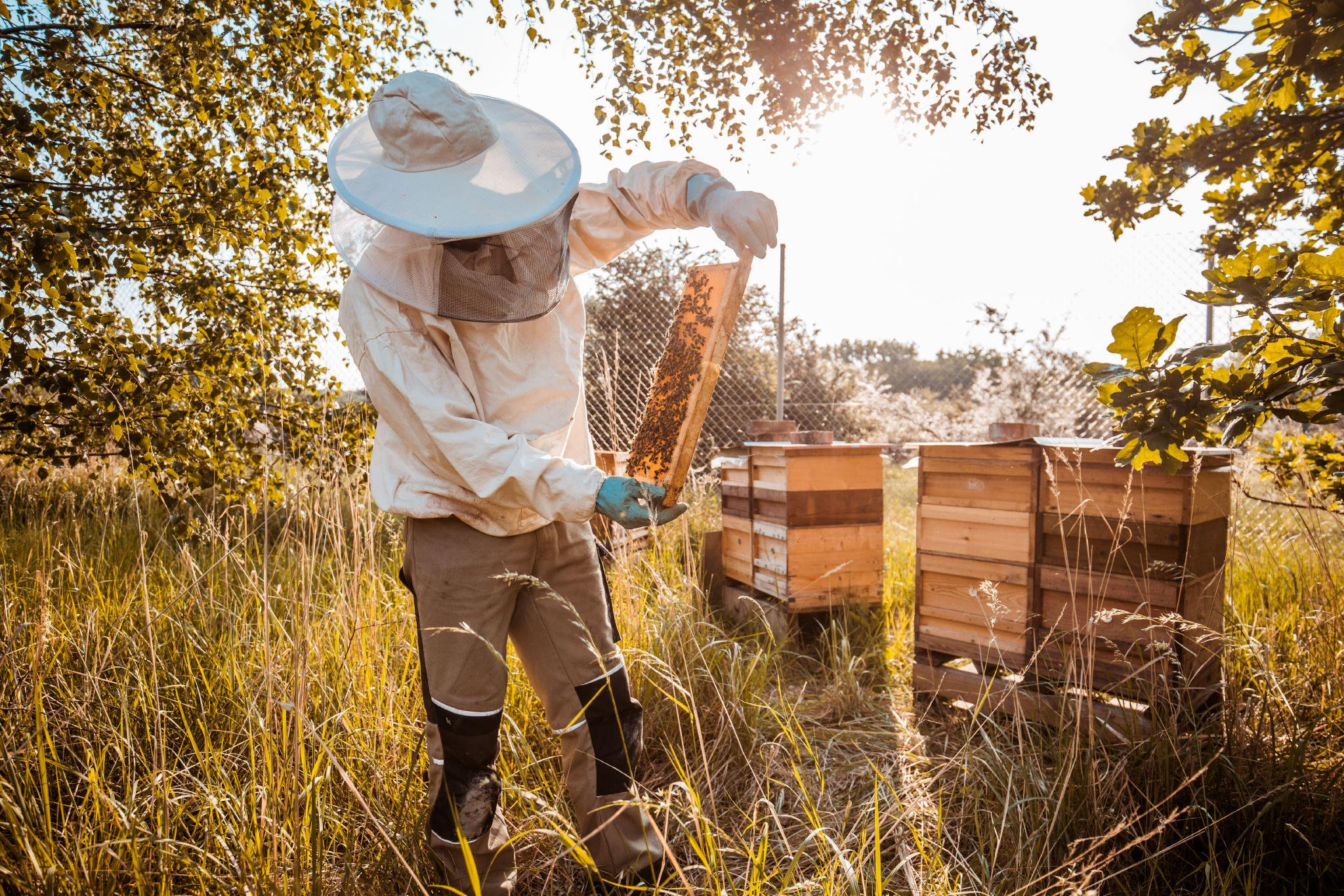
如今,保時捷萊比錫工廠依然在投資和擴產的過程中。工廠總經理介紹說,2017年很多生產流程還是人工,現在則是自動化。與此同時,他們也對員工做更多的電氣化和數字化軟件培訓。“自動化”和“數據化”並不一定會帶來人工崗位的大量缺失,也可能是一個提升技能的機遇。